For all new developments, the welding technology manufacturer relies on intuitive, self-explanatory controls to efficiently design the man-machine interface. Use of the new, intelligent PM welding torch, for example, brings this interface directly into the welder’s hand and, therefore, even closer to the weld seam. This means that the user always has an eye on important parameters such as gas or wire supply while welding.
With the digitisation of all welding machines with highly intelligent microprocessors, interfaces, and network connections, EWM meets all the requirements for Big Data process data collection. This information can be displayed in the user’s primary systems via standardised industrial interfaces, such as OPC- UA. This allows for machine efficiency analyses and preventative maintenance.
MIG/MAG welding machine from EWM makes welding Industry 4.0 capable.
In keeping with the “Welding 4.0” slogan, EWM will introduce its conclusive answer to the urgent challenge of “Industry 4.0” for the welding industry – the new multi-processMIG/MAGpulseweldingmachineseries Titan XQ puls. Its key innovation: it has comprehensive digital network capabilities and can therefore unlock significant untapped potential for savings throughout the entire process chain. In addition, it also includes all the efficiency-enhancing, innovative welding processes from EWM as standard in the machines at no extra charge. At the same time, the Titan XQ puls offers the characteristics typical of EWM – durability, robust design and high power reserves.
Digital networking under the Industry 4.0 buzzword will soon be a must for any manufacturing company. EWM makes its customers future-proof with the Titan XQ puls. In addition to many other digital functions, the machines are network-compatible via the Welding 4.0 welding management system ewm Xnet. Welding procedure specifications can be transmitted directly from the planning office to the Titan XQ puls – paperless and including all parameters. At the same time, the ewm Xnet software also takes over the often obligatory bureaucracy – Titan XQ puls is able to deal with a large part of the previously time-consuming welding documentation automatically with ewm Xnet, traceable down to the last detail for each individual run. Thanks to Titan XQ puls, considerable increases in efficiency and quality can be achieved with EWM Xnet throughout the entire added-value process of a welding company.
Robust for tough applications
EWM has designed its new Titan XQ puls welding machine for tough applications, especially in steel, shipbuilding and vehicle construction. It is splash-proof (IP23) even under extreme conditions in rain, frost and snow in the temperature range from –25 °C to +40 °C. The 350 A, 400 A, 500 A and 600 A power variants are initially offered as decompact versions with the separate lightweight 13 kg wire feeder, which has also been newly developed.
The inner values of the welding machine additionally attest to the EWM quality at its latest stage of development: the Titan XQ puls inverters are designed for hard continuous operation in 3-shift operation. They guarantee a duty cycle of 80% (Titan XQ puls 350,400 and 500). The generous dimensioning of power semiconductors and cooling, in particular, promises a long service life and no trouble with the heart of the welding machines.
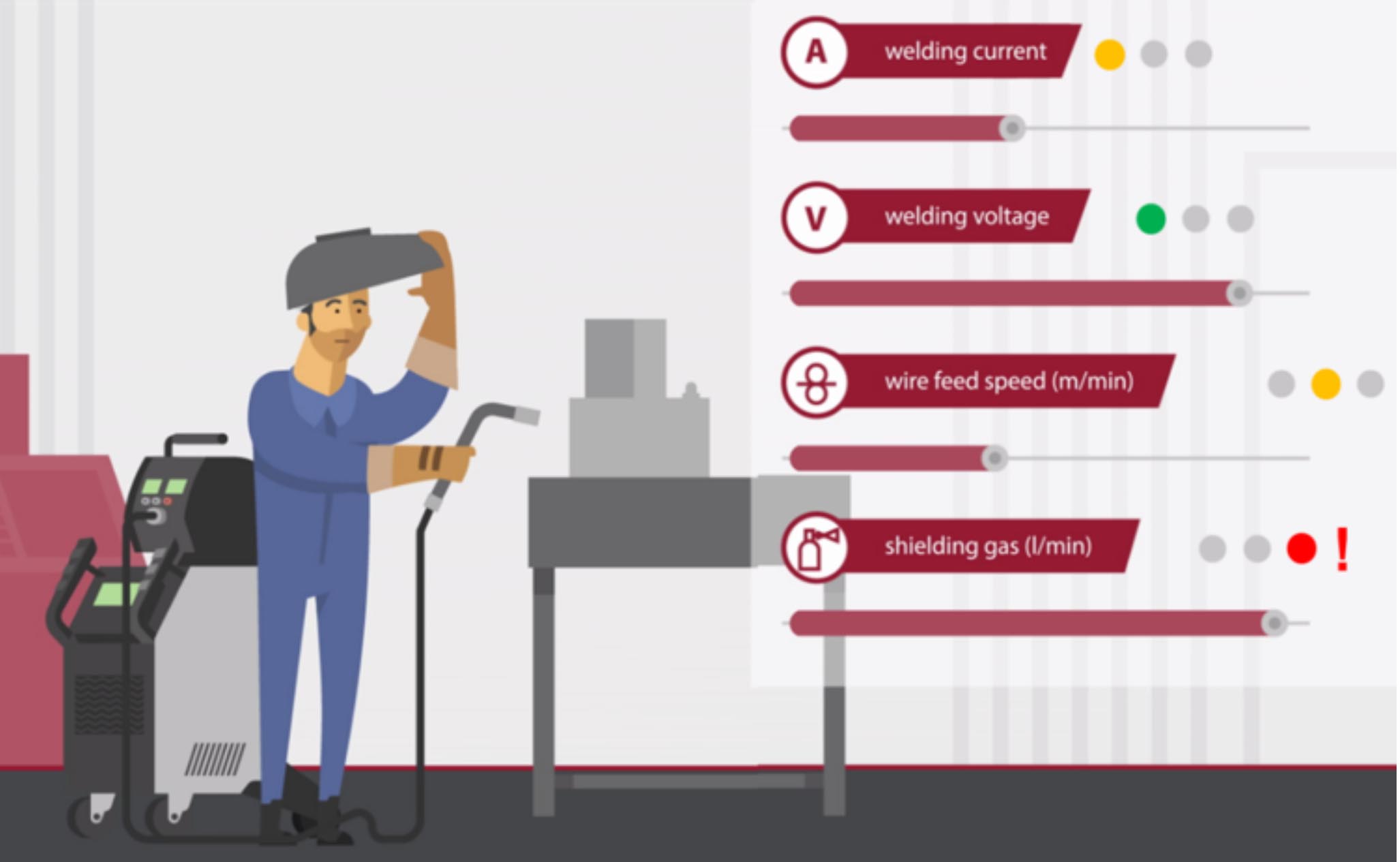
New welding torches and controls
The user can look forward to innovations in everyday operation. This includes four versions of the brand new PM welding torch to choose from. Control buttons, graphic display and LED illumination of the working area as well as the new, ergonomically shaped grip with rubber insert promise comfortable, fatigue-free welding even in positional welding.
Other innovations come in the form of three controllers to choose from, which EWM is presenting with Titan XQ puls. The premium model is called Expert XQ 2.0. Only welding procedures, material, gas and wire diameter need to be selected via click-wheel operation in the plain text display – the characteristic that exactly matches the welding task automatically follows.
All welding procedures as standard
All innovative welding procedures from EWM are included in the purchase price of the Titan XQ puls as standard and can be selected via any of the offered controls. Regardless of whether for thin or thick sheet applications, filler, final or root passes, or in positional welding – the Titan XQ puls perfectly fulfils any welding task on low to high-alloy steel and aluminium.
Available as standard are forceArc, forceArc puls, wiredArc, wiredArc puls, coldArc, coldArc puls, rootArc, rootArc puls, positional welding as well as MIG/MAG pulse and standard arc. Not only do they make it easier to produce welding seams of a consistently high quality, they can also save a considerable amount of time and material.
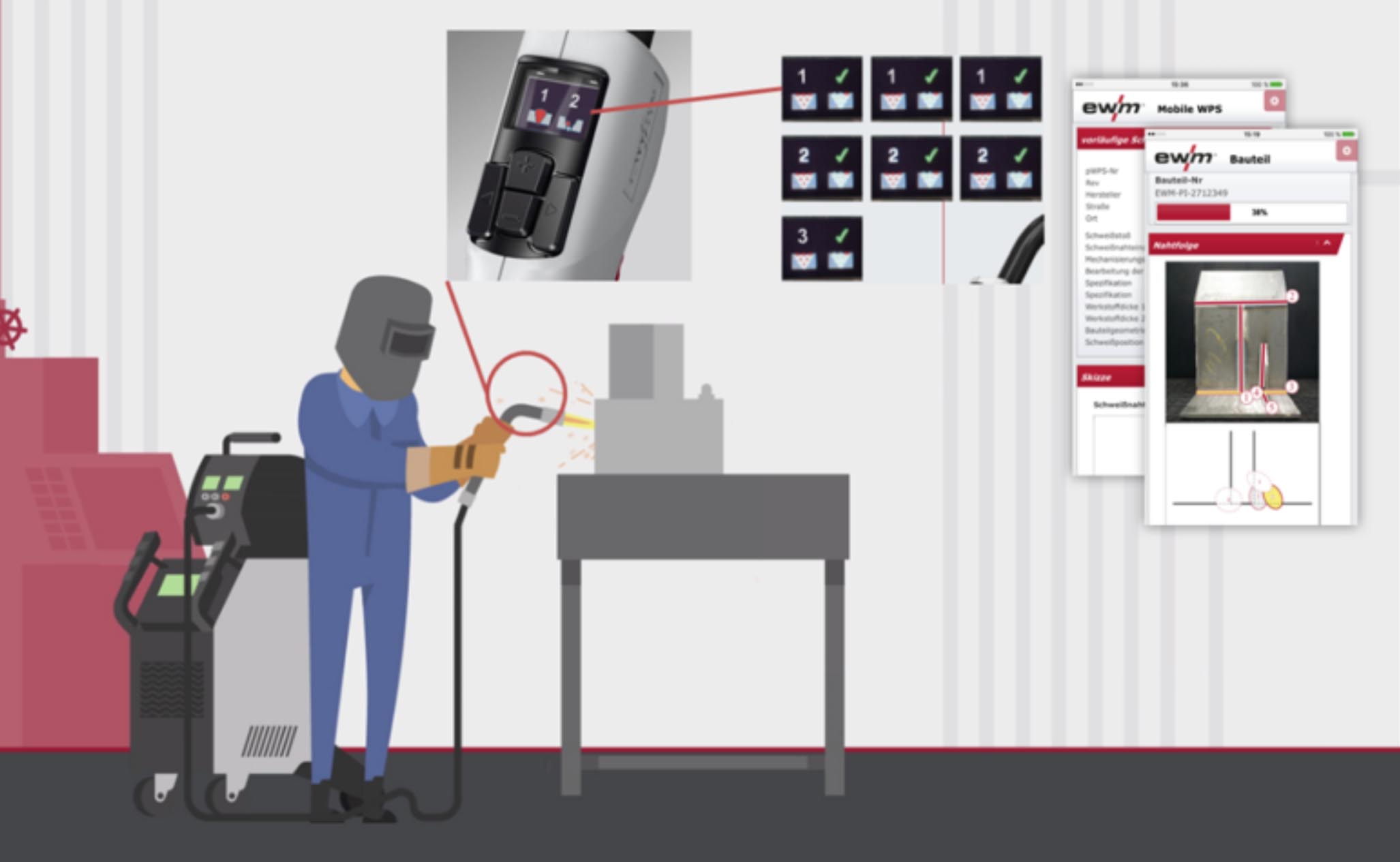
Source:
EWM, “PM Titan XQ”, EWM: Cutting and Welding PR Titan XQ puls increases efficiency and saves money, 25 September. 2017, https://www.ewm-group.com/ presse/3_GB_EWM-cutting-and-welding_PR_TitanXQ. pdf
EWM, “PM Welding-Industrie 4.0”, EWM: Cutting and Welding PR Welding-Industrie4.0 EWM accompanies customers on the path towards Industry 4.0, 25 September. 2017, https://www.ewm-group.com/ presse/5_GB_EWM-cutting-and-welding_PR_Welding- Industrie40.pdf